Finest Practices for Preventing Weld Undercut: Grasping the Fundamentals
Grasping the Art of Welding: How to Stay Clear Of Undercut Welding Issues for Flawless Construction Outcomes
Performance and precision are paramount on the planet of welding, where also the slightest blemish can compromise the architectural honesty of a fabricated piece. One usual difficulty that welders face is undercutting, a defect that can lead and compromise a weld joint to costly rework. By recognizing the source of undercut welding and carrying out reliable techniques to avoid it, welders can elevate their craft to new levels of quality (Preventing weld undercut). In the search of remarkable construction results, mastering the art of welding to prevent undercut concerns is not just a skill yet a necessity for those pursuing excellence in their job.
Understanding Undercut Welding
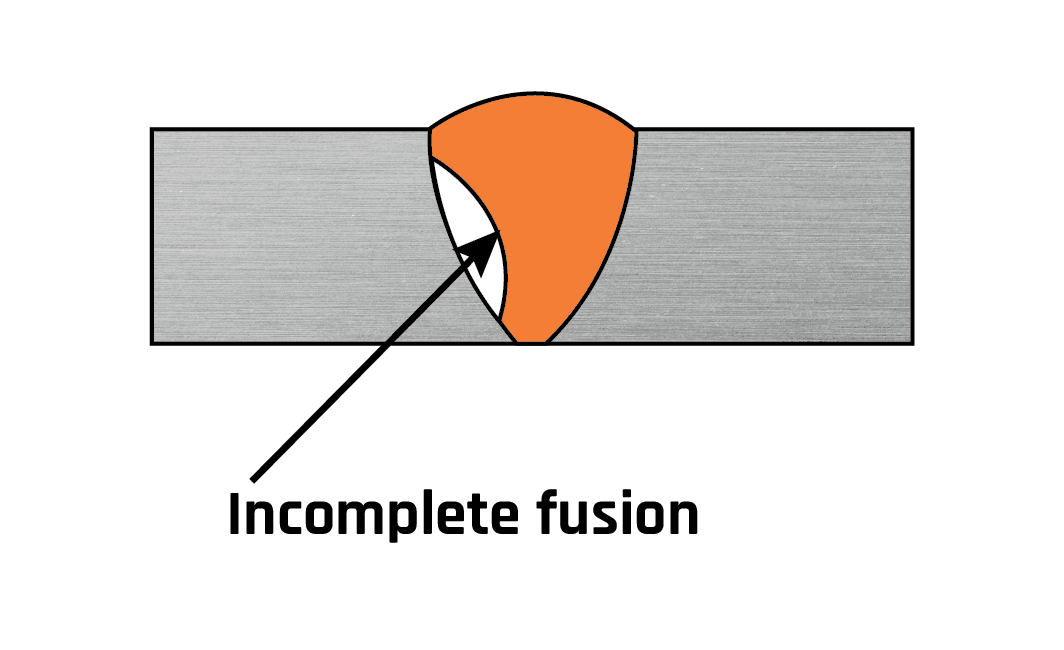
To prevent undercut welding, welders must ensure appropriate welding parameters, such as adjusting the current, voltage, travel speed, and keeping the right electrode angle. By recognizing the causes of undercut welding and implementing preventive actions, welders can accomplish high-grade, structurally audio welds.
Reasons For Undercut in Welding
Recognizing the factors that add to undercut in welding is necessary for welders to produce premium, structurally audio welds. Inadequate welding wrong or existing welding speed can likewise contribute to undercut. Recognizing these causes and executing proper welding methods can aid prevent damaging concerns, guaranteeing solid and durable welds.
Strategies to Avoid Undercutting

To mitigate the risk of damaging in welding, welders can utilize strategic welding techniques aimed at improving the high quality and stability of the weld joints. In addition, utilizing the proper welding technique for the particular joint setup, such as weave or stringer beads, can add to lowering damaging.
Furthermore, proper joint preparation, including guaranteeing clean base materials devoid of pollutants and making use of the proper welding consumables, is important in stopping undercut defects. Employing back-step welding strategies and regulating the weld grain profile can additionally help distribute warmth evenly and lessen the danger of undercut. Normal examination of the weld joint during and after welding, in addition to implementing high quality guarantee procedures, can aid in identifying and dealing with undercutting problems quickly. By executing these strategies faithfully, welders can attain flawless fabrication results with marginal undercut issues.
Value of Proper Welding Parameters
Picking and preserving proper welding specifications is essential for achieving successful welds with marginal issues. Welding specifications describe variables such as voltage, current, take a trip rate, electrode angle, and protecting gas flow price that straight influence the welding procedure. These criteria have look at this site to be thoroughly adjusted based on the sort of product being bonded, its thickness, and the welding discover this info here technique utilized.
Proper welding parameters guarantee the correct amount of warm is put on melt the base steels and filler material uniformly. If the specifications are established too expensive, it can result in excessive warm input, creating spatter, distortion, or burn-through. On the other hand, if the criteria are as well low, insufficient blend, absence of infiltration, or damaging might take place.
Quality Guarantee in Welding Workflow
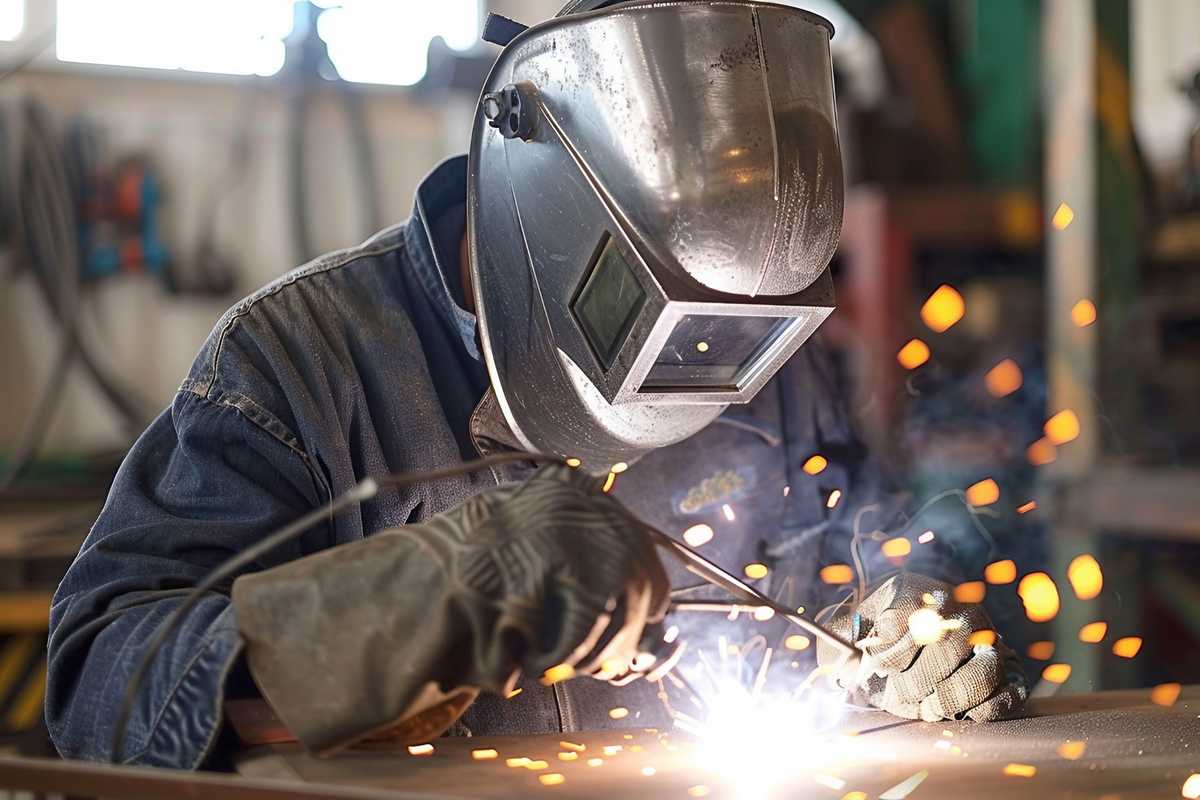
Conclusion
In final thought, grasping the art of welding calls for a detailed understanding of undercut welding, its causes, and techniques to avoid it. By making sure proper welding specifications and implementing high quality guarantee methods, remarkable construction outcomes can be achieved. It is essential for welders to consistently pursue quality in their welding procedures to avoid undercut issues and create top quality welds.
Undercut welding, this website an usual defect in welding procedures, takes place when the weld metal does not properly fill the groove and leaves a groove or clinical depression along the bonded joint.To avoid undercut welding, welders need to ensure correct welding parameters, such as changing the existing, voltage, traveling speed, and keeping the proper electrode angle. Poor welding inaccurate or current welding rate can also add to damage.To minimize the danger of undercutting in welding, welders can use strategic welding methods aimed at enhancing the top quality and honesty of the weld joints.In verdict, mastering the art of welding needs a comprehensive understanding of undercut welding, its reasons, and strategies to prevent it.